Retaining walls are one of the most common structural tools for landscaping. A retaining wall is a wall used in landscaping as a stabilising structure for sloping soil. No matter the type of retaining wall, it must be sturdy enough to disperse pressure caused by sloping. If you are thinking of using a retaining wall for your landscaping project, familiarise yourself with the disadvantages of retaining walls, before making the commitment to install one.
- Retaining walls are one of the most common structural tools for landscaping.
- No matter the type of retaining wall, it must be sturdy enough to disperse pressure caused by sloping.
Vertical Cracks
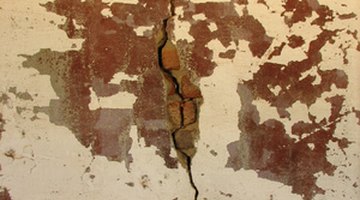
Some retaining walls begin developing vertical cracks, such as in poured concrete. This is often due to excessive pressure or wide changes in temperature. In order to prevent these vertical cracks, provide plenty of good drainage, which can often be expensive to accomplish.
Failing Foundation

Retaining walls need extensive drainage resources to prevent moisture, but they also require a strong foundation. Some retaining walls will not be able to retain high amounts of pressure from soil, such as bricks walls. This often results in crumbling bricks or a failing foundation.
Termites
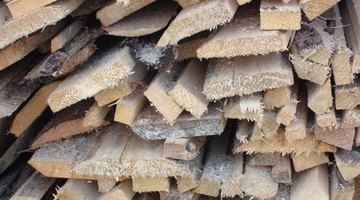
Retaining walls also can attract termites to your property, as is often the case when timber is used as a retaining wall. Termites can nest inside rotting timber and near moulded areas. Correcting this problem can be expensive, if you have to use termite monitoring and treatment devices.