Physics is the study of the forces acting on and between objects. While statics is the study of forces on objects at rest, dynamics concerns the forces (pushes or pulls) imposed on objects when they change their velocity (accelerate). Mass defines an object's resistance to velocity change, and weight describes an object's attractive force toward Earth's centre due to the acceleration from Earth's gravity acting on its mass. Acceleration is the rate at which velocity changes. Dynamic load refers to a force imposed on a system because it is accelerating an object in a given direction.
- Physics is the study of the forces acting on and between objects.
- While statics is the study of forces on objects at rest, dynamics concerns the forces (pushes or pulls) imposed on objects when they change their velocity (accelerate).
Define the application for calculating dynamic load; the weigh scale on an elevator is a good method in which to do so. A 150-pound adult standing on a scale on an elevator at ground level notes their 150-pound reading as they push the button for the 20th floor. The elevator ascends at a rate of 16 feet-per-second. Knowing that it takes 4 seconds from a dead stop to accelerate to this velocity, you can calculate the dynamic load that will read out on the scale during the 4-second upward-acceleration period.
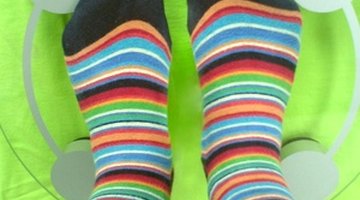
Calculate the instantaneous rate of acceleration. Because it takes the elevator 4 seconds to reach the 16 foot-per-second upward velocity, the average rate of acceleration is: 16 feet-per-second/4 seconds = 4 feet-per-second, per-second, or 4 feet-per-second^2.
Calculate the dynamic load to the elevator during upward acceleration by solving Newton's Second Law of Physics, F (force) = m (mass) X a (acceleration). Substituting the stated values into this (dynamic load) formula, F = 68 Kilogram X ([32-feet + 4-feet]/sec^2/acceleration of gravity [32 feet-per-sec^2]) = 76.5 Kilogram. The scale would read 68 Kilogram while at rest on the ground floor and 76.5 Kilogram during the 4 seconds accelerating upward to 16 feet-per-second.
- Calculate the instantaneous rate of acceleration.
- Calculate the dynamic load to the elevator during upward acceleration by solving Newton's Second Law of Physics, F (force) = m (mass) X a (acceleration).
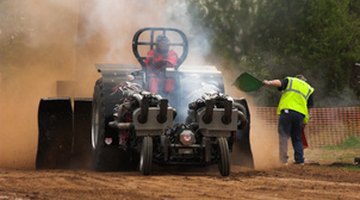
Define the horizontal dynamic load application. In this example, a 3,000-pound vehicle accelerates from zero to 60mph in 7.2 seconds. With this information, you can calculate the dynamic load to the vehicle's drive wheels.
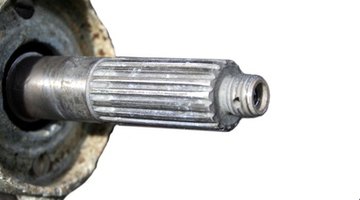
Calculate the vehicle's rate of acceleration. Sixty mph equates to 88 feet-per-second, divided by 7.2 seconds, yielding 12.22 feet-per-sec^2.
Calculate the dynamic load to the drive wheels by solving the F = m x a formula, which is Newton's Second Law of Physics. Substituting stated values, F = 1361 Kilogram x 12.22-feet/sec^2/32.2-feet/sec^2 or 3,000 x 0.3795 = 62.8 Kilogram, representing the dynamic load exerted by the drive-wheel tire treads against the road to accelerate the car.
TIP
Smooth, steady acceleration presents much lower loads to machines and human joints than jerky motion and helps longevity greatly.
WARNING
Falling from a height of just a few feet can inflict serious damage or injury because of the significant multiplication of forces from gravity.